Excellent product even better than expected.
Neodymium Disc Magnet - 25mm x 2mm | Teflon Coating
Product code: 20007T

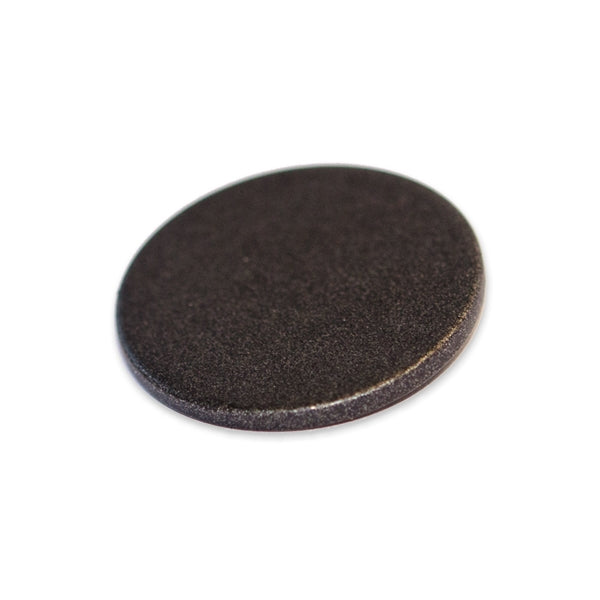

Prices are GST Incl.
Volume pricing available on requestAustralia's Leading Supplier
Shipping Worldwide*
30 Day Returns
Same Day Dispatch*

Magnetic Product Description:
This Teflon coated Rare Earth Disc has a diameter of 25mm and a height of 2mm. It has a magnetic flux reading of 1043 Gauss and a pull force of 3.7 kilos. It is identified by AMF magnet part number 20007T.
Uses for our Teflon coated Disc Magnets:
Industrial storage and steel fabrication businesses supply a range of products and services sometimes tailor made to suit their clients’ individual needs. Using these Teflon coated 25mmx2mm magnets these companies build lockers, cabinets, material handling devices, shelving and mezzanine floors, pallet racks and loading dock equipment.
Building custom made or made to order machines and equipment presents its own very real difficulties, very different to plucking a mass produced item from existing stock. Designers and the tradespeople filling these orders need a variety of options when considering the durability, desirability and user friendliness of anything they design and construct. These magnets, along with many others create options other methods and materials simply cannot match for simplicity and efficacy. The predictability, reliability and cost effectiveness of magnetisation also helps keep the costs of design and construction under control. Controlling production costs is vital in any business, particularly when estimating in advance the price to the client of producing custom built equipment.
No FAQ available

Magnetic Product Description:
This Teflon coated Rare Earth Disc has a diameter of 25mm and a height of 2mm. It has a magnetic flux reading of 1043 Gauss and a pull force of 3.7 kilos. It is identified by AMF magnet part number 20007T.
Uses for our Teflon coated Disc Magnets:
Industrial storage and steel fabrication businesses supply a range of products and services sometimes tailor made to suit their clients’ individual needs. Using these Teflon coated 25mmx2mm magnets these companies build lockers, cabinets, material handling devices, shelving and mezzanine floors, pallet racks and loading dock equipment.
Building custom made or made to order machines and equipment presents its own very real difficulties, very different to plucking a mass produced item from existing stock. Designers and the tradespeople filling these orders need a variety of options when considering the durability, desirability and user friendliness of anything they design and construct. These magnets, along with many others create options other methods and materials simply cannot match for simplicity and efficacy. The predictability, reliability and cost effectiveness of magnetisation also helps keep the costs of design and construction under control. Controlling production costs is vital in any business, particularly when estimating in advance the price to the client of producing custom built equipment.
No FAQ available